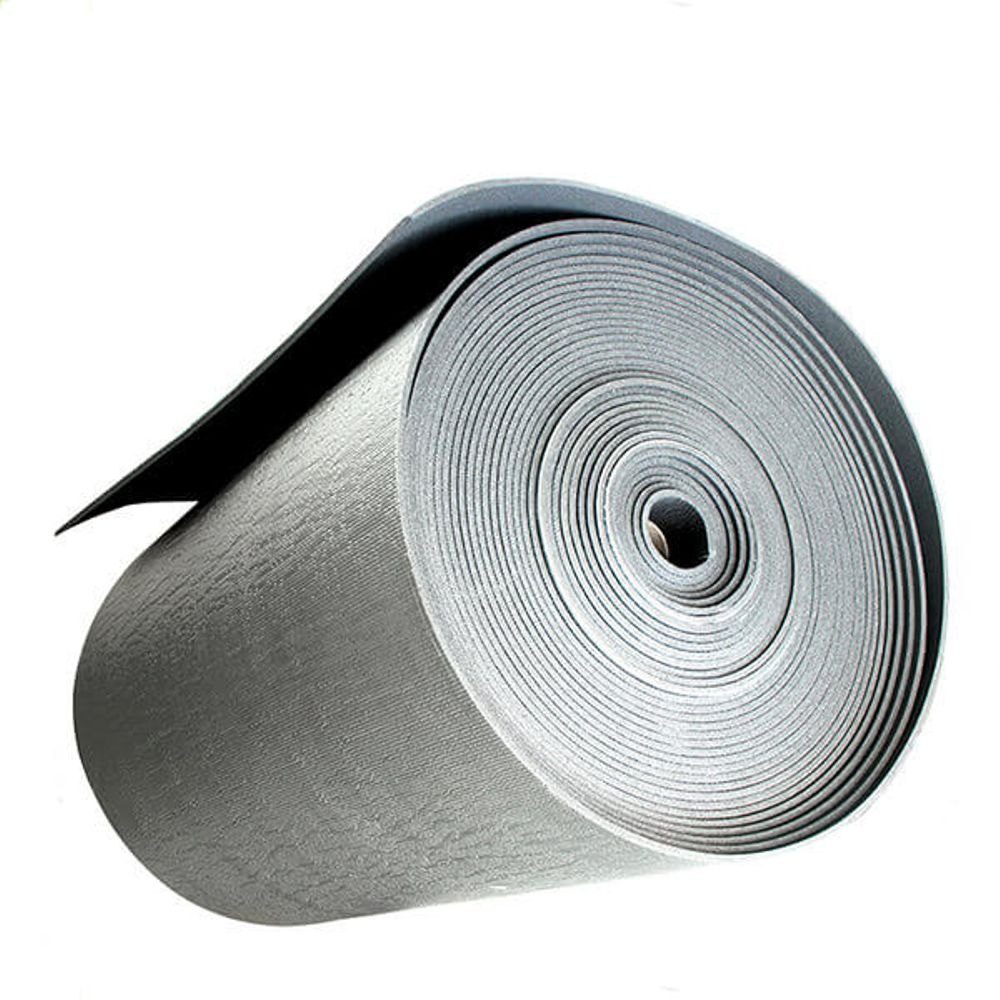
What is thermal insulation?
Thermal insulation is a fundamental concept employed in various industries to control heat transfer and maintain optimal thermal conditions within systems. Whether dealing with solid objects, fluids, or gases, the primary goal is to introduce a barrier that minimizes the exchange of heat. This practice is crucial across diverse sectors, such as energy, industrial, medical, and more, where thermal efficiency is paramount for optimal performance.
In the energy sector, thermal insulation plays a pivotal role in conserving energy and enhancing the efficiency of processes. Industrial applications heavily rely on insulation to regulate temperatures in manufacturing processes, ensuring product quality and machinery functionality. In medical contexts, thermal insulation is utilized to maintain specific temperature ranges for sensitive equipment or storage of medical supplies.
The complexity of these applications necessitates the use of various insulation technologies tailored to specific thermal challenges. Engineers and professionals in these industries carefully select insulation materials based on their thermal conductivity, durability, and compatibility with the intended environment.
Effective thermal insulation not only conserves energy but also contributes to sustainability efforts by reducing the overall environmental impact of energy-intensive processes. By minimizing heat transfer, industries can optimize their operations, improve system reliability, and achieve cost savings in the long run.
How does thermal insulation work?
Thermal insulation is a fundamental concept employed in various industries to control heat transfer and maintain optimal thermal conditions within systems. Whether dealing with solid objects, fluids, or gases, the primary goal is to introduce a barrier that minimizes the exchange of heat. This practice is crucial across diverse sectors, such as energy, industrial, medical, and more, where thermal efficiency is paramount for optimal performance.
In the energy sector, thermal insulation plays a pivotal role in conserving energy and enhancing the efficiency of processes. Industrial applications heavily rely on insulation to regulate temperatures in manufacturing processes, ensuring product quality and machinery functionality. In medical contexts, thermal insulation is utilized to maintain specific temperature ranges for sensitive equipment or storage of medical supplies.
The complexity of these applications necessitates the use of various insulation technologies tailored to specific thermal challenges. Engineers and professionals in these industries carefully select insulation materials based on their thermal conductivity, durability, and compatibility with the intended environment.
Effective thermal insulation not only conserves energy but also contributes to sustainability efforts by reducing the overall environmental impact of energy-intensive processes. By minimizing heat transfer, industries can optimize their operations, improve system reliability, and achieve cost savings in the long run.
Double-wall insulation
Gases exhibit poor heat conductivity due to the significant distance between their molecules. This property makes them effective insulators. One practical application of this principle is seen in double-wall insulation systems, where air or other gases are trapped between two layers of solid materials to create a thermal barrier.
A notable example of double-wall insulation is found in insulated glass units or thermal windows. These windows are designed with two or three layers of glass, and the space between them is sealed. The sealed space is filled with gases like argon, which are known for their low thermal conductivity. The purpose of introducing these gases is to minimize convective and conductive heat exchange through the window, thus enhancing its insulating properties.
The key advantages of double-wall insulation, particularly in windows, include:
- Reduced Heat Transfer: The trapped gas serves as a barrier that hinders the transfer of heat between the interior and exterior of a building. This contributes to better energy efficiency by minimizing the loss or gain of heat through windows.
- Enhanced Insulation: Compared to single-pane windows, double-wall insulation provides superior insulation, helping maintain a more consistent indoor temperature and reducing the workload on heating or cooling systems.
- Condensation Control: The insulated space between glass layers helps control condensation by maintaining a closer temperature to the indoor environment, preventing moisture from forming on the interior surfaces of the window.
- Improved Comfort: By minimizing heat exchange, double-wall insulation contributes to a more comfortable indoor environment, with fewer temperature variations near windows.
In summary, the use of double-wall insulation, especially in windows, capitalizes on the insulating properties of gases to create an effective thermal barrier. This technique aligns with the broader goal of improving energy efficiency and enhancing the comfort of buildings by controlling heat transfer.
Vacuum insulation
Vacuum insulation is indeed a highly effective method for thermal insulation, providing superior temperature control compared to double-wall insulation with gas-filled gaps. The key principle behind vacuum insulation is the removal of air molecules from the space between two walls. By creating a vacuum, convective and conductive heat transfer are significantly reduced, leading to better thermal efficiency.
The absence of air minimizes heat transfer mechanisms, as air is a good conductor of heat. Without air, there is no convection or conduction, which are major contributors to heat loss. This makes vacuum insulation particularly effective in environments where precise temperature control is crucial.
This technology is often employed in applications where traditional insulation materials might not suffice due to performance or durability concerns. Advanced vacuum insulation is sought after in systems that require the highest possible thermal energy efficiency, such as cryogenic storage, ultra-low temperature applications, or high-performance insulation for buildings and appliances.
It’s worth noting that while vacuum insulation provides excellent thermal performance, maintaining a vacuum over time can be challenging due to potential leaks. Therefore, the design and construction of vacuum-insulated systems must carefully consider factors like material integrity, sealing mechanisms, and long-term reliability.
Insulating against radiation
Absolutely, reflective materials with low emissivity are commonly used for insulation against thermal radiation. Emissivity is a measure of how well a material emits thermal radiation. Materials with low emissivity are effective at reflecting and minimizing the emission of radiant heat.
Aluminum foil is a classic example of a reflective material with low emissivity. It is often used in various applications, such as in building insulation, packaging, and even in cooking to reflect and retain heat. The shiny surface of aluminum is effective at reflecting radiant heat.
In more advanced and specialized applications, especially those involving ultra-high temperatures and critical conditions, more sophisticated reflective materials may be used. These materials are designed to withstand extreme environments and provide excellent reflective properties at specific wavelengths.
Reflective insulation is particularly useful in scenarios where traditional insulation methods may not be as effective. For example, in spacecraft or satellites, reflective materials are used to manage the intense thermal radiation from the sun. Similarly, in industrial processes involving high temperatures, such as in furnaces or aerospace applications, advanced reflective materials play a crucial role in minimizing heat transfer via radiation.
The choice of reflective material depends on the specific requirements of the application, including temperature, durability, and the desired range of radiation reflection.
Example of insulating against radiation